螺杆连云港冷水机组首要由螺杆紧缩机、冷凝器、蒸发器、膨胀阀及电控体系组成。水冷单螺杆连云港冷水机组制冷原图如下:
(一)双螺杆制冷紧缩机
双螺杆制冷紧缩机是一种能量可调式喷油紧缩机。它的吸气、紧缩、排气三个接连进程是靠机体内的一对相互啮合的阴阳转子旋转时发生周期性的容积改变来实现。一般阳转子为自动转子,阴转子为从动转子。
首要部件:双转子、机体、主轴承、轴封、平衡活塞及能量调理设备。
容量15~100%无级调理或二、三段式调理,采取油压活塞增减载方法。惯例采用:
径向和轴向均为滚动轴承;敞开式设有油分离器、储油箱和油泵;封闭式为差压供油进行光滑、喷油、冷却和驱动滑阀容量调理之活塞移动。
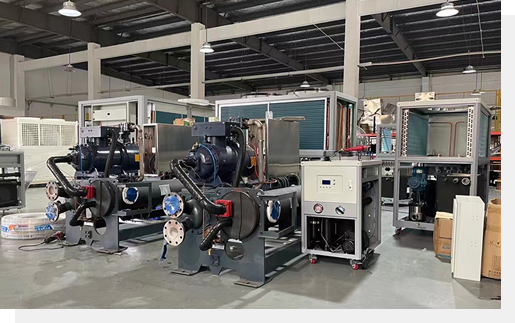

紧缩原理:
吸气进程:气体经吸气口别离进入阴阳转子的齿间容积。
紧缩进程:转子旋转时,阴阳转子齿间容积连通(V型空间),因为齿的 互相啮合,容积逐渐缩小,气体得到紧缩。
排气进程:紧缩气体移到排气口,完结一个工作循环。
(二)单螺杆制冷紧缩机
利用一个自动转子和两个星轮的啮合发生紧缩。它的吸气、紧缩、排气三个接连进程是靠转子、星轮旋转时发生周期性的容积改变来实现的。
转子齿数为六,星轮为十一齿。
首要部件为一个转子、两个星轮、机体、主轴承、能量调理设备。
容量能够从10%-100%无级调理及三或四段式调理。
紧缩原理:
吸气进程:气体通过吸气口进入转子齿槽。随着转子的旋转,星轮依次进入与转子齿槽啮合的状况,气体进入紧缩腔(转子齿槽曲面、机壳内腔和星轮齿面所形成的密闭空间)。
紧缩进程:随着转子旋转,紧缩腔容积不断减小,气体随紧缩直至紧缩腔前沿转至排气口。
排气进程:紧缩腔前沿转至排气口后开端排气,便完结一个工作循环。因为星轮对称安置,循环在每旋转一周时便发生两次紧缩,排气量相应是上述一周循环排气量的两倍。
单螺杆制冷紧缩机与双螺杆制冷紧缩机特点之比较
双螺杆制冷紧缩机的特点:
1、需喷油紧缩(也可采用少量喷液)。一旦失油时或许发生金属与金属的啮合冲突,影响工作和转子寿数。
2、转子径向负荷及轴向推力大,尤其是轴向推力非常大,需体积和强度大的轴承或平衡活塞来抵消轴向力,轴承使用寿数受影响。
3、油不仅用于螺杆阴阳转子之间之冷却、密封,并作光滑及动力传递(25~60%的动力)。工作时一般需继续起动油泵。油耗量大,油路体系杂乱。
4、一般轴承寿数为20,000~30,000小时,30,000小时即需大修。
5、首要部件仅为活塞式制冷紧缩机的十分之一。
6、单级紧缩比高。低温工况时能够采取独有的经济器结构,节能性好,但成本相应有所提高。
7、紧缩机效率比单螺杆略高。
8、单机头**制冷量较单螺杆大。
9、对液击不灵敏,能够湿行程工作。

单螺杆紧缩机之首要特性及优点:
1、使用寿数长,可靠性极高。
根据下列理由故有很长经用寿数(一般25年以上):
(a)螺杆转子与星轮间的啮合紧缩为金属与非金属。转子资料为六齿钢制涂铝保护层,星轮为十一齿52层增强纤维复合强化资料。能够实现柔性零空隙触摸密封。
(b)零部件及易损件极少,首要运动部件仅为五件,一个转子,两个星轮,两个滑阀。
(c)因为转子径向和轴向受力完全平衡,故轴承径向和轴向推力极小,轴承可靠性极高,轴承规划寿数达100,000小时,为双螺杆的3~5倍。
(d)工作时采取喷液取代喷油,密封、光滑和冷却效果更好,啮合阻力低, 具有经济有效之光滑。无油光滑方法,不需要杂乱的油路体系,只须少量冷冻机油,油路较双螺杆简明。
(e) 20,000小时后方需查看,30,000~40,000小时后方需较大保养。星轮能够单独拆开,修理简洁。
(f)因为星轮处于一种柔性承载状况,能够调整它与主转子之间的空隙,所以液击不灵敏,能够湿行程工作。
(g)半封闭单螺杆电机液体冷却,坚持长时间冷却状况,电机寿数长。
(h)因为转子受力平衡,轴封负荷极度小,寿数长,远高于双螺杆紧缩机轴封寿数。
2、效率高。
(a)转子与星轮的"零空隙"配合,**程度减小走漏损失和压力损失,效率大幅度提高。
(b)半封闭单螺杆电机液体冷却,电机效率高。
3、因为六齿转子与十一齿星轮啮合时涣散和减少了排气脉动,从而使排气平稳,加上交替啮合又有效地排除正弦波音,所以噪音低沉、易隔音。一般比同级双螺杆低0.8~5dB(A)(3ft)。
4、工作时极度平稳,振动值低于0.14Ips。双螺杆紧缩机则明显高于此值。
5、现场便于修理,连云港冷水机可从顶部或底部拆开星轮进行修理。